COMPANY HISTORY
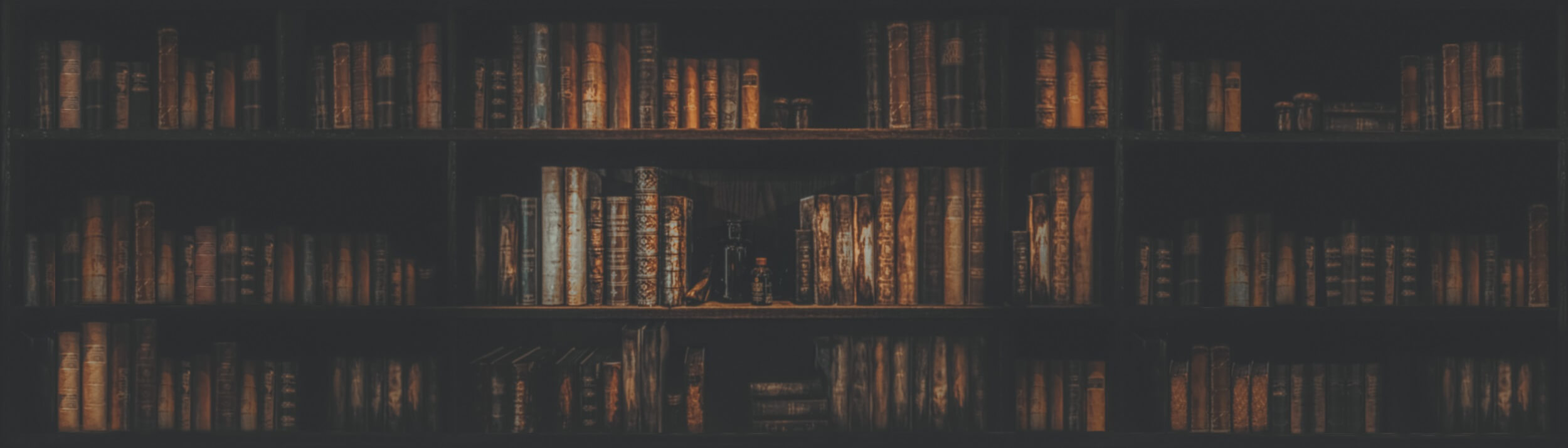
The company’s history date back to July 1994 when the Suresh Abraham working together with Jose had only two manually operated injection moulding machines.
As the plastic injection moulding technology grew, we seized the opportunity to expand our operations by incorporating more advanced and better machines. Today, we are a leading producer and supplier of plastic components built through advanced injection moulding techniques. We have also grown beyond this to add other services as the needs of our clients expanded. These include pad printing, ultrasonic welding, orbital riveting process, and customised product assembly, among others.
Sujo Plast Through The Years
July 1994: The Birth of Sujo Plast
The company began its operations in July 1994 when Suresh Abraham and Jose had only a small outlet with only two manual injection moulding machines. In the beginning, the demand for plastic moulded components was not stiff as such, but our resilience and determination saw the company through.
January 1995 – January 2000: Sujo Plast Expands Through More Manual Injection moulding Machines
Six months down the line in January 1995, Sujo Plast started to experience a higher influx of orders from automotive parts manufacturers, toy sellers, and other plastic component dealers. To cope with the growing demand, Suresh and Jose decided to acquire 15 additional manual injection moulding machines. This also meant that there was more expertise needed, and therefore the pioneers decided to onboard a group of well-trained plastic injection moulding experts into the team.
The company continued to receive even more orders and signed new contracts with renowned brands. In April 1999, Sujo Plast onboarded INFAC INIDA (Pvt) LTD through a deal that saw us supply them with plastic components for automotive parts. We became a crucial part of INFAC’s growth through the early 2000s.
By the start of the new millennium, in January, Sujo Plast gave expansion a shot by introducing its first-ever semi-automatic injection moulding machine. This welcomed more growth as now production was not solely dependent on human input.
January 2000 – January 2009: Sujo Plast Goes Fully Automatic
As the years went by, our company signed more contracts and expanded its supply chain beyond India into India’s business partner countries. But our only semi-automatic injection moulding machine could not hold up to the growing demand for our products. We responded to this by adding 15 additional semi-automatic injection moulding machines.
In June 2007 We acquired our first automatic injection moulding machine.
Two years down the line, Sujo Plast through its lead engineers had to seek improved ways of creating better quality plastic injection moulding products. As the market competition grew stiffer, we had to prove to our clients that we are a superior manufacturer by adding another automatic injection moulding machine, the Super Master 50T.
August 2010 – Sujo Plast Becomes ISO Certified
Since the beginning, our company has always kept the promise of delivering high-quality products that surpass market standards. But the only way of proving this was to acquire an international quality assurance certification. And in August 2010, we became fully ISO 9001:2008 certified.
With this certification, we saw major business contracts coming our way. In September 2010, Sujo Plast onboarded PREETHI Kitchen Appliance Limited into our list of clients. This did not end there, 9 months later, in June 2011, we started supplying our plastic injection moulding products to Electromags Automotive Products Pvt Ltd.
January 2011 – February 2021: Sujo Plast Expands its Engineering Division
In our pursuit of excellence, Sujo Plast became SQ Certified in January 2012 after the completion of the SQ audit by HMI. This meant that we were a company with a quality mark on our forehead. Our recognition in the plastic moulding industry grew even further.
It is during this period that Sujo Plast upgraded its machinery by acquiring 9 automatic injection moulding machines. With a well-equipped engineering division, we expanded our product line by starting the Orbital Riveting Process in March 2017.
After monitoring the success of the Orbital Riveting Process, Sujo Plast welcomed a new product, Pad Printing in July 2018. As our operations expanded, we saw a need to update our quality assurance profile, and in August of the same year, we acquired the ISO 9001:2015 certification.
With great power comes more responsibility. Sujo Plast had become a giant and a force in plastic injection moulding manufacturing. We had to live up to this by proving our efficiency by creating our own tool room in April 2019.
Since our portfolio was growing much quicker than we anticipated, we had to upgrade our machinery to stay up to date with the market demand. In November 2019, Sujo Plast made a big move by introducing the Motan dehumidifying setup to serve 2 moulding machines. This in a way, helped our production process live up to the promise of delivering quality plastic products by ensuring products are adequately dried.
To show proof of our competence, we were SQ Certified in December 2019.
November 2020 – June 2022: The Modern, Efficient Sujo Plast
We have come a long way, and our resilience and determination to outshine the global standards have seen us through thick and thin. Even as the pandemic struck the world, Sujo Plast had to ensure its operations are not affected. We kept different brands from around the world moving by providing a consistent supply of plastic injection moulded products.
In November 2020, Sujo Plast introduced the Ultrasonic Welding (USW) process, a more advanced industrial process that saw us expand our operations even further. With this advanced technology, we saw different global brands approach us to become their sole supplier of plastic moulded products. These include Sharda Motor, Gesco Healthcare, Sudarshan Auto Electrical Components Pvt ltd, Philips, and more.
Fast forward to May 2022, Sujo Plast became a modern plastic injection moulding manufacturer with state-of-the-art equipment. We introduced the more efficient a 50T vertical moulding machine which saw our production processes become more seamless.
We are still pursuing greater heights and this is evident through the consistent expansion of our machinery. We have lived up to the promise of delivering high-quality products by updating our machine inventory with the a 15T Hydro Pneumatic Press machine. We endeavour to achieve even more and make life better.